Glass-Like Metal Performs Better Under Stress
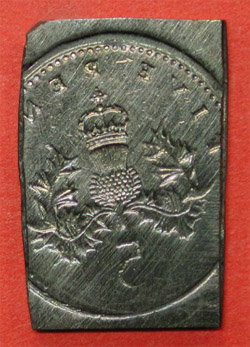
Futuristic alloys called amorphous metals could someday combine the strength and electrical conductivity of ordinary metals with the versatility and low cost of plastic. Separate papers in the 27 May PRL describe two new experimental materials in this class–one super-strong, the other super-malleable–suggesting that an amorphous metal having both properties may be physically possible. The super-strong material is also the first amorphous metal that, like steel, gets harder rather than softening under stress. Amorphous metals could revolutionize several industries, possibly making cars cheaper and safer, and nano-components easier to finely shape.
Steel is strong but difficult to shape because it requires very high temperatures to bend or pour into molds. Amorphous metals promise to combine strength with the versatility of plastic. Their structure is disordered or “amorphous” at the atomic scale, like plastic or glass, whereas ordinary metals such as steel are assemblies of small crystals. These crystals can halt the propagation of cracks, so amorphous metals–lacking crystals–are often as brittle as glass when they are stressed. Steel, by contrast, becomes harder after being stressed: As every self-respecting Samurai or Nordic-epic hero knows, lots of hammering makes a good sword.
By adding just the right amounts of aluminum atoms to a copper-based alloy, a team led by Jürgen Eckert of the Technical University of Darmstadt in Germany and Wei Hua Wang of the Chinese Academy of Sciences in Beijing has now produced the first amorphous material that gets harder under stress. Like some similar materials, it’s stronger than conventional steel and has a higher resistance to scratching and corrosion.
The researchers believe that the material’s ability to harden under stress is somehow related to its ability to bend without breaking, called ductility, which it shares with some similar materials. The ductility may result from nanometer-scale atomic clusters that can prevent crack propagation, just as small crystals do in steel. These particles show up under the electron microscope, says team member and Darmstadt graduate student Jayanta Das, “but we don’t know their structure.” The researchers were able to make two-millimeter-thick sheets, which could be suitable for cell phone or laptop computer casings.
Mixing in the right ingredients was also the key to the new malleable material that Wang and a different team, writing in a second paper, call “metallic plastic.” Like real plastic or glass, amorphous metals soften gradually when heated, instead of abruptly changing to a liquid state. That’s what makes it possible, for example, to blow glass. In previous amorphous metals, the transition began at temperatures of several hundreds, if not thousands, of degrees Celsius. But the new cerium-based material can be molded in hot water–at less than 100 degrees. That could make it useful for nanotechnology applications such as data storage. “It’s easy to make complicated nanoscale features,” Wang says, similar to the bits on CD surfaces.
William Johnson of the California Institute of Technology in Pasadena says that the ideal amorphous metal would consist of cheap ingredients and would combine the properties of both new materials. Although cerium is expensive, the metallic plastic demonstrates that low-temperature malleability is physically possible, Johnson says. And while you don’t want hot water to turn your laptop into goo, similar materials with slightly higher transition temperatures could be developed, possibly allowing many car parts to be cast cheaply like plastic. He says an improved version of the copper-based material might be good for aircraft components or even vehicle chassis, which must deform to absorb the energy of a collision, but must also become progressively stiff during the crunch.
–Davide Castelvecchi
Davide Castelvecchi is a freelance science writer in Rome.